Primary vs secondary techniques for NOx reduction: What are the differences and how do you pick?
by Aalborg Energie Technik a/s on Feb 15, 2023 12:06:48 PM
There are many reasons why biomass boiler operators should want to reduce the NOx emissions of their plants. In addition to the health and environmental dangers of NOx, there are current and future emission limits that can have consequences for existing environmental permits. Whether you’re motivated by the desire to leave a better planet for future generations or simply need to fulfill legislation, the end goal is the same.
There are many ways to reduce NOx emissions. In general terms, there are two main strategies that can be pursued, known as primary techniques and secondary techniques.
Primary vs secondary techniques
When we talk about primary techniques of NOx reduction, we are referring to the methods that can be used to avoid the formation of NOx during combustion. This can be done by optimising the combustion conditions of your plant - factors such as fuel, technology, and temperature. Primary measures are generally applicable and should be utilised to the largest possible extent.
While primary techniques aim to prevent or minimise the formation of NOx, secondary techniques are means of reducing the NOx that has already been created.
The principle for the most common secondary NOx reduction methods is to inject a reducing agent (usually ammonia or urea) into the flue gas:
- At higher temperatures (around 850 - 1100°C), the NOx reduction is a spontaneous reaction
- At lower temperatures (typically 150 - 260°C), the NOx reduction requires a catalyst to
facilitate the reaction.
Primary methods for NOx reduction:
- Low excess air ratio
- Staged combustion (fuel and air staging)
- Reducing combustion air temperature
- Advanced control system
- Flue Gas Recirculation (FGR)
- Water injection.
Secondary methods for NOx reduction:
- Standard Selective Non-Catalytic Reduction (SNCR)
- Advanced Selective Non-Catalytic Reduction (SNCR)
- Selective Catalytic Reduction (SCR)
- Hybrid SNCR and SCR.
How to choose the right technique
The above methods for NOx reduction are based on the European Commission’s Best Available Techniques Reference Document for Large Combustion Plants.
In many cases, the most effective approach to reducing your plant’s NOx emissions will be to combine both primary and secondary techniques. AET works closely with our customers to take into consideration the setup of each individual boiler plant to determine which NOx reduction methods would be most effective.
Read how AET has helped customers reduce NOx emissions
A number of physical variables influence which solutions will work best, including:
- The boiler and furnace design
- The design and configuration of the burners
- The reducing agent used – urea solution or ammonia water?
- The feasibility of injecting and distributing reducing agents into the flue gas at the right temperatures
- The operating conditions of the boiler, including load variations, fouling, etc.
- The fuel type and characteristics
- Flue gas characteristics like composition, velocity, flow direction and temperature profile.
There are also legislative factors to consider:
- The emission limit values (NOx, CO, SO2, NH3 etc.) that need to be met
- Potential trade-offs with other emissions (notably CO)
- Argumentation of the use of Best Available Techniques (BAT).
And of course, there are financial considerations as well:
- CAPital EXpenditures (CAPEX) vs. OPerating EXpenses (OPEX)
- How future-proof is the solution?
- How long will it take to see a return on investment?
Taking the above factors into consideration, AET strives to understand the specific needs and concerns to suggest the best possible tailored solution for NOx reduction.
To learn more, be sure to read our more detailed articles about primary techniques and secondary techniques. You can also download our e-book 'NOx Reduction for biomass- and fossil fuel-fired boilers'.
Do you need help with your project?
Our experts are ready to assist you. Fill out the form below and we will get back to you as soon as possible.
Contact us
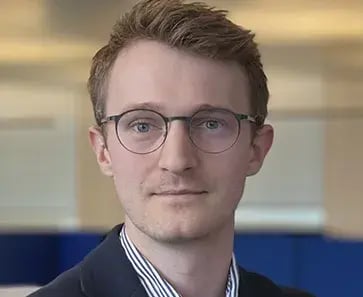
David Kjølby Krøger
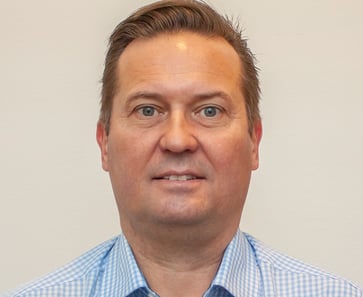