Primary techniques for NOx reduction
by Aalborg Energie Technik a/s on Feb 15, 2023 1:22:45 PM
There are a number of available solutions for reducing the amount of NOx that is generated during combustion in a boiler plant. Strategies for reducing emissions at the point of generation are known as primary techniques.
The most effective primary techniques include the design and optimisation of a boiler’s combustion system, installing an advanced control system, recirculating flue gas, and injecting water into the furnace.
The design of a boiler’s combustion system can be optimised for efficiency and to reduce the emissions of dust, soot, carbon monoxide (CO) and NOx. This article takes a closer look at primary NOx reduction techniques.
Low excess air ratio
One effective way of both optimising your operations and reducing your NOx emissions is to focus on lowering the oxygen content in the flue gas.
The formation of NOx is highly dependent on the prevalence of oxygen in the combustion process. An effective measure of NOx reduction, therefore, is to design the combustion system with a low excess air ratio. For existing boilers, it is possible to optimise the current combustion process to lower the excess air ratio.
Some combustion technologies have greater potential to reduce oxygen content than others.
For example, step-grate boilers typically have an oxygen content of 5 to 8% and need a furnace refractory to have an efficient combustion process with an acceptable CO level.
Spreader stoker and travelling grate boilers (SSTG) have a combustion process with the lowest oxygen content possible – roughly 2%. This type of boiler is highly efficient and has the lowest in-house power consumption.
Bubbling fluidised bed (BFB) boilers typically have an oxygen level of 4 to 5%, while circulating fluidised bed boilers (CFB) have an oxygen level of 3 to 5%. FB boilers have low combustion temperatures, which can result in harmful N2O emissions.
Advantages of a low excess air ratio:
- Typical NOx reduction of 5 to 25%
- Simple way to optimise the combustion of an existing system
- Reduced oxygen content will increase boiler efficiency
- Reduced oxygen content will also reduce power consumption
- May lead to lower CO emissions.
Disadvantages of a low excess air ratio:
- Can be difficult to implement in existing plants due to physical constraints
- In some cases, it may lead to higher CO emissions.
Staged combustion
Staged combustion techniques are also efficient primary techniques for avoiding the formation of NOx.
The fuel staging technique is based on lowering the flame temperature to create several combustion zones within the furnace, each with different injection levels of fuel and air.
With air staging, the oxygen content within the furnace is adjusted into several combustion zones. This can involve a primary (sub-stoichiometric) zone, a secondary (over-stoichiometric) zone and optimally a tertiary (final burnout) zone.
A prerequisite to achieving the benefits of staged combustion is having continuous and uniform fuel and air injection:
- A fuel dosing system can consist of a dosing bin, chutes, rotary valves and spreader stokers. This fuel dosing system has to operate with extremely high accuracy and uniform fuel dosing and must be independent of fuel particle geometry in order to avoid the injection of fuel lumps into the furnace.
- Primary air injection must be independent of the fuel layer to have a stable combustion process. In order to keep the flame temperature down, the primary air should account for 35-50% of the total air supply for biomass combustion.
- Secondary/tertiary air injection must sequence the air injection and ensure full combustion at a low temperature. Depending on the furnace design and fuel injection system, it may be necessary to have different air injections on the front and rear walls.
Advantages of staged combustion:
- Typical NOx reduction of 5 to 30%
- Effective measure to reduce CO emissions
- Simple way to optimise the combustion of an existing system
- Reduction of O2 can increase boiler efficiency and reduce power consumption.
Disadvantages of staged combustion:
- Can be difficult to implement in existing plants due to physical constraints.
Reducing combustion air temperature
Another primary measure to reduce NOx emissions is to avoid pre-heating the combustion air in a regenerative or steam air preheater.
Advantages of reducing the combustion air temperature:
- Typical NOx reduction of 2 to 5%
- Helps to simplify operations.
Disadvantages of reducing the combustion air temperature:
- Air preheating might be required due to other emissions (e.g. CO)
- Air preheating might be desired for achieving high cycle efficiency
- The effect on NOx generation might be limited compared to other measures.
Advanced control system
Implementing a computer-based automatic system that uses high-performance monitoring to control the combustion parameters can improve efficiency. In fact, an advanced control system is a prerequisite for cost-effective NOx reduction.
The advanced control system provides a high level of infrastructure health information and handles both plant operation and control functions as well as safety-related functions.
The high level of information ensures that operational tasks can be performed with a full overview, thereby allowing operators to make better decisions and take better actions.
Operating data will be archived, allowing operators to identify consumption and performance patterns for potential optimisation.
The system utilises high-level instruments that allow for enhanced fault finding and supports the possibility of remote support and online troubleshooting.
Advantages of an advanced control system:
- Provides a process overview and allows for immediate intervention
- Minimises OPEX due to lower O2 and lower NOx reducing agent consumption
- Increases availability and decreases maintenance costs, due to remote support from experts and predictive maintenance.
Disadvantages of an advanced control system:
- Requires employee training.
Flue gas recirculation (FGR)
Recirculating the flue gas to the combustion zone will lower the combustion temperature and oxygen content, which will generally postpone the combustion and thereby reduce NOx formation.
Advantages of flue gas recirculation:
- Typical NOx reduction of 10 to 30%
- Can increase boiler efficiency due to lower O2
- Can contribute to less slagging in the furnace.
Disadvantages of flue gas recirculation:
- NOx reduction potential depends on combustion conditions
- Increased power consumption for fans
- Lower furnace residence time
- Can reduce boiler efficiency due to higher O2
- May require more flue gas flow through the boiler.
Water injection
NOx reduction can be challenging if the flue gas temperatures are too hot. Water can be used as a diluent to reduce the combustion temperature and thereby directly reduce thermal NOx. The temperature reduction can be done in general or locally to reduce temperature peaks. In the case of SNCR, water injection can provide the necessary operating conditions for utilising SNCR as a secondary technique of NOx reduction.
Advantages of water injection:
- Typical NOx reduction of 5 to 10%
- Very low CAPEX
- Fast implementation.
Disadvantages of water injection:
- Expensive water consumption
- Decreased residence time in the furnace
- Lower boiler efficiency
- Changes in droplet sizes can affect the penetration depth.
In addition to these techniques for reducing NOx formation during combustion, there are also ways of reducing the NOx that has already been created.
Do you need help with your project?
Our experts are ready to assist you. Fill out the form below and we will get back to you as soon as possible.
Contact us
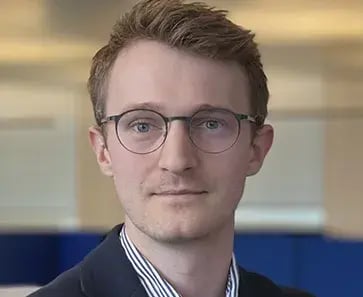
David Kjølby Krøger
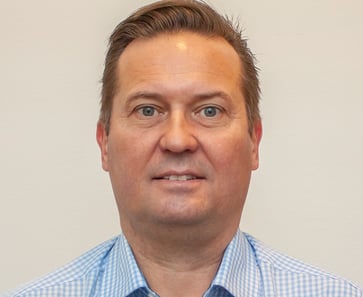