How biomass residues helped a German sugar factory decarbonise
by Aalborg Energie Technik a/s on Mar 30, 2023 2:25:30 PM
As part of its ambition to completely phase out coal, the major European sugar manufacturer Pfeifer & Langen decided in 2020 to decarbonise its sugar factory in Könnern, Germany.
After an initial meeting with AET, Pfeifer & Langen decided to carry out a combustion test and a load test to determine how to best convert the power source of its boilers from coal to biomass residues.
The tests were successfully performed with bio-pellets and thanks to the AET SNCR DeNOx test kit, it was confirmed that NOx emissions did not exceed Germany’s strict regulations.
RELATED ARTICLE: Primary vs secondary techniques for NOx reduction:
What are the differences and how do you pick?
This approach allowed Pfeifer & Langen to make a business-oriented decision to convert their existing boilers to biomass through a process that would have minimal design and operational risks and result in a more competitive solution.
AET was engaged to do the fuel conversion on the two existing travelling grate boilers (2 x 80 t/h, 85 bar, 500°C), a significant element of Pfeifer & Langen’s overall decarbonisation journey.
‘A solid plan and budget’
“By selecting AET, we saw a partner that demonstrated a step-by-step approach with a successful combustion test, a solid plan and a budget that would not jeopardise our production security throughout our campaign,” Mathias Herbrig, Production Manager at Könnern, said.
Taking the Könnern factory’s production schedule, in which juice is produced from January to May and sugar is produced from September to January, into account, an original plan was drawn up to convert one boiler to natural gas and the second boiler to biomass.
However, when the invasion of Ukraine in 2022 made it harder and significantly more expensive to get natural gas, the management of Pfeifer & Langen concluded that both boilers should operate on biomass.
The modified plan for converting the boilers to biomass consisted of:
- Fuel feeding: The existing coal feeding system was re-used. However, an automatic three-level security system from the emergency shut-off valve to the furnace inlet was installed to secure against potential backfire through the pellets.
- Pressure part: establish biogas burners; 2x4 MWth.
- Air and flue gas system: Changes were made in the primary and secondary air system, including flue gas recirculation and combustion of waste process gas from the sugar factory.
- Standard AET SNCR DeNOx system: Urea-based SNCR with one level of injection lances to secure NOx emissions below 100 mg/Nm3 @ 6%O2.
To learn more about fuel conversion and to read how other companies have emulated Pfeifer & Langen’s success, download our newest e-book ‘Fuel Conversion: Converting from coal to biomass and residues to improve sustainability’.
Do you need help with your project?
Our experts are ready to assist you. Fill out the form below and we will get back to you as soon as possible.
Contact us
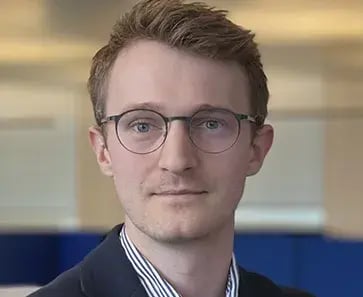
David Kjølby Krøger
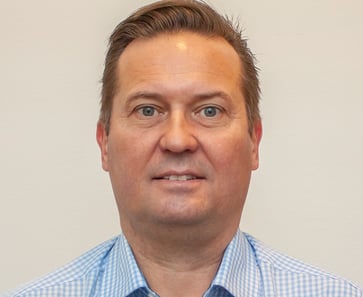