From coal to biomass: Clean district heating, fuel flexibility and operational savings
by Aalborg Energie Technik a/s on Mar 30, 2023 2:07:05 PM
Verdo Energy Systems is one of Europe’s top suppliers of sustainable biomass for district heating plants. In the Danish city of Randers, Verdo built a district heating plant in 1982 that consisted of two coal-fired steam boilers (2 x 95 MWth, 111 bar, 525oC) from Aalborg Boilers and one common steam turbine (52 MWe). The cogeneration plant supplies electricity and hot water to the roughly 60,000 residents of Randers.
As part of its commitment to sustainability, Verdo decided to reuse some of the industrial waste from the surrounding areas to fuel its boilers.
Two AET-assisted retrofits
In the early 2000s, AET helped Verdo retrofit the Randers cogeneration plant with an AET Dust Firing System that would allow it to use biomass such as meat and bone meal, olive stones, shea nuts, sunflower pellets and bio pellets as a fuel source. Adding the AET Dust Firing System to the existing boilers resulted in greater fuel flexibility and allowed the plant to operate in co-firing mode with a mix of at least 50% coal and up to 50% biomass. The boilers could also operate on 100% coal in single mode – or any combination in between.
To further decarbonise its operation, an additional substantial retrofit was carried out in 2008-2009 that allowed the boilers to fire on 100% biomass. A flue gas condensation system was also installed, while a separate wood-firing system implemented at the same time gave Verdo the option to continue to fire coal if and when needed.
The existing Vølund travelling grate was re-used and AET Combi Spreaders were added. Thanks to the AET Combi Spreader Stoker, the Randers plant was able to fire 100% biomass or 100% coal or any combination in between, e.g., 70% biomass and 30% coal.
While the initial co-firing project did not involve major modifications of the furnace and heating surfaces, the conversion to 100% biomass necessitated an extension of the furnace in order to keep a full load on the boilers. Some of the existing heating surfaces were re-designed and a new economiser tube bank was added. The existing grates were relocated accordingly and the secondary/tertiary air system was further extended with additional injection levels.
Verdo’s CHP plant now burns wood residues as well as dusty fuels using the AET Dust Firing System.
Flexibility and low prices
A transition from coal to biomass can be challenging, as biomass can cause corrosion and a potential build-up of slag. To minimise these risks, CFD modelling was made of the combustion, furnace and heating surfaces to identify the temperature profile and concentration of potassium chloride (KCl). After this modelling, it was decided to change the material for the hanging superheaters (SH2 and SH3) from carbon steel to stainless steel.
With the two AET-assisted retrofits, Verdo’s Randers plant now provides a greener source of electricity and hot water to city residents.
“The two retrofits have given us fuel flexibility. We can now use whatever fuel is available on the market at a low price. The rebuild of our boilers in 2008-2009 has been functioning as expected and to our full satisfaction. We are exceedingly pleased with our long-term experience using AET Combi Spreaders”, said Henrik Bøgh Nielsen, Division Director, Verdo.
To learn more about fuel conversion and to read how other companies have emulated Verdo’s success, download our newest e-book ‘Fuel Conversion: Converting from coal to biomass and residues to improve sustainability’.
Do you need help with your project?
Our experts are ready to assist you. Fill out the form below and we will get back to you as soon as possible.
Contact us
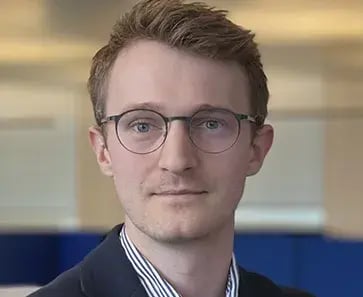
David Kjølby Krøger
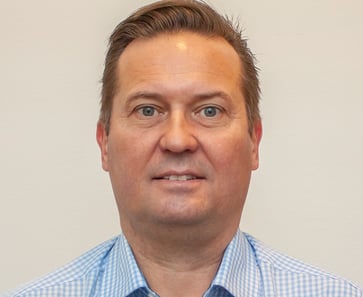