What are the challenges and impacts of fuel properties used to power chemical plants?
by Aalborg Energie Technik a/s on Jan 6, 2023 1:49:50 PM
If you are a chemical company that has opted to move away from fossil fuels in order to decarbonise your operations, you should be aware of the challenges and impacts of the different fuels that you can use to power your chemical plant.
To assess whether a fuel is suited for firing or co-firing in a biomass boiler, it is important to understand the basic, chemical, physical and ash properties of the fuel. The properties have a significant influence on the fuel handling system, the fuel dosing and the firing system, the grate, the air injection, the combustion area, the boiler, and the flue gas cleaning system.
Below are some essential details about different fuel properties and their significance that you need to know when designing your fuel handling system and biomass-fired boiler:
Lower heating value
A lower heating value depends on the elementary fuel composition, ash content and fuel moisture, and is calculated according to the Boie formula.
Fuel moisture
A higher fuel moisture content will reduce the combustion temperature and influence the combustion process and combustion system response, and the overall plant performance. Excessive moisture content can lead to increased CO2 emissions, unstable or poor combustion and increased carbon content in the ash, ultimately requiring the use of the burner to stabilise combustion.
In an existing boiler plant, a higher fuel moisture content will increase the flue gas flow, and lead to higher flue gas velocities, higher in-house power consumption and eventually may require a reduction of the load.
For a new plant, a high moisture content will increase the size of the air and flue gas system, increase the capacity of air preheating, sizing and positioning of secondary and tertiary air system as well as flue gas recirculation, and with extremely high moisture content. It can be an advantage to dry the fuel.
Elementary composition (C, H, O)
The elementary composition of the fuel is used for calculating the amount of combustion air and flue gas flow.
Ash content and foreign matter
Excessive ash content will increase wear in the flue gas path. If the fuel contains large amounts of foreign matter, this may cause disturbances and blockages in the fuel handling system. Aluminium in the fuel, in solid form, can also block the air nozzles in the primary air system.
High content of ash and foreign matter may lead to metal separation in the fuel handling and/or ash system, increased ash system size and low flue gas design velocities (due to high particle flow on heating surfaces).
Nitrogen (N)
The nitrogen content in the fuel has a significant influence on the amount of nitrogen oxide (NOx) emitted, and on the choice and capacity requirements of the flue gas denitrification system.
With a high nitrogen content in the fuel, there are many options to address this:
- Optimising the combustion system
- Reducing O2
- Flue gas recirculation
- Non-catalytic (SNCR DeNOx)
- Catalytic (SCR DeNOx)
- Etc.
Sulphur (S)
Excessive sulphur content can lead to excessive use of the flue gas desulphurisation adsorbent (typically hydrated lime or sodium bicarbonate) before a bag filter. A high sulphur content also increases the risk of corrosion at low temperature economiser surfaces due to sulphuric acid attacks. A high sulphur content will normally increase the ash melting point and may counteract fouling and slagging.
Therefore, appropriate feed water and flue gas temperatures have to be selected, according to the calculated sulphur dewpoint. Desulphurisation adsorbent type and the amount have to be selected in accordance with the required emissions. Particle recirculation for desulphurisation around the bag filter is to reduce the use of the adsorbent.
Chlorine (Cl)
Chlorine is the main determinant of the flue gas side corrosion risk. Molten salt corrosion takes place underneath salt melts of heavy metal chloride on e.g. furnace walls and superheater pipes, especially lead (Pb) chlorides and zinc (Zn) chlorides and including eutectic melts.
High-temperature chlorine-induced corrosion takes place during sulphation of alkali metal (K, Na) chlorides in the ash deposits. High chlorine content also increases the use of flue gas desulphurisation adsorbent and may furthermore lead to increased formation of dioxins/furans (PCDD/PCDF) in the presence of copper (Cu).
With high chlorine content, the following solutions can be applied:
- Cladding of the furnace walls (e.g. Inconel)
- Using stainless or higher alloyed steel for the superheater
- Ensuring the appropriate choice of live steam pressure and temperature
- Adding powdered activated carbon (PAC) for flue gas cleaning
- Choosing a desulphurisation adsorbent
- Applying particle recirculation for desulphurisation around the bag filter
Alkalis (Na, K), Silicon (Si), and Phosphor (P)
Increased contents of the above elements tend to decrease the ash melting temperatures and increase the level of slagging and fouling in the furnace and of ash deposits on the superheater tubes, especially in connection with increased levels of chlorine.
- For new plants with high Na, K, Si and P, you might consider:
- Increasing the tube pitch in high-temperature superheaters
- Using tube economisers (instead of finned tubes)
- Using grate-fired boilers, as they are not sensitive to low ash melting points – which means there’s no bed sintering
Alkaline earth metals (Ca, Mg)
Increased alkaline earth metal contents tend to increase ash melting temperatures and lower the risk of slagging and fouling on the heating surfaces.
Heavy Metals (Zn, Pb, Cd, Hg)
Increased contents of heavy metal, for the most part, decrease the ash melting temperature, resulting in formation of hard deposits. In the presence of alkalis and chlorine, increased heavy metal contents heighten the risk of high temperature corrosion, and molten salt corrosion of the furnace walls and superheater tubes.
Excessive lead content in the fuel can lead to the formation of hard deposits on the superheater and ultimately block the flue gas path which must be removed mechanically.
- For plants with high contents of heavy metals, the following solutions can be applied:
- Cladding of the evaporator walls (e.g. Inconel)
- Using stainless or higher alloyed steel for the superheater
- Ensuring the appropriate choice of live steam pressure and temperature
- Using powdered activated carbon (PAC) for flue gas cleaning to comply with emission limit values
Ash melting behaviour and ash composition
Certain ash-forming elements tend to decrease the ash-melting temperature (as described in the points above), and often eutectic melts have even lower melting temperatures (several elements in combination). This needs to be considered in the design of the boiler, including the design of heating surfaces and cleaning equipment.
Physical properties
Consider physical properties such as whether particle size, bulk density, etc. is appropriate for fuel handling and the fuel dosing system.
Fuel handling and bridging properties
In general, when it comes to fuel handling properties, we think it’s important that you bear in mind whether the fuel is free-flowing, sticky, compressible, odourless, and so on.
When it comes to bridging properties, consider whether the fuel is bridging – particulate matter forming a solid bridge over an opening, thereby clogging and obstructing the flow.
Further examples of the properties of the biomass and residues and their challenges are shown in the table below.
Finally, fuel types that differ significantly in physical or handling properties might not be suitable for mixing in all cases. If fuel mixing is not feasible, another option is to install a supplementary system for co-firing such fuels.
To find out about the many varieties of biomass and residues, read our blog “Which biomass and residues should power your chemical plant?”.
To find out more about which biomass and residues should power your chemical plant, download our free e-book.
Do you need help with your project?
Our experts are ready to assist you. Fill out the form below and we will get back to you as soon as possible.
Contact us
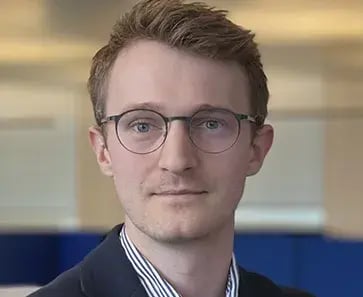
David Kjølby Krøger
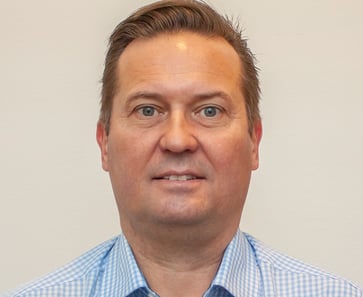