7 reasons it’s better to convert an existing coal-fired boiler than installing a new one
by Aalborg Energie Technik a/s on Mar 30, 2023 2:09:25 PM
There are many good reasons to convert a coal boiler to biomass and residues, which are a cleaner and more cost-effective, efficient and reliable source of steam and power than fossil fuel.
Similarly, there are several reasons why it makes more sense to convert an operational coal-fired unit than to install a new biomass-fired boiler. Conversion requires a lower capital investment (CAPEX), enables the most condensed time schedule and makes smart use of existing assets.
Here are seven reasons why fuel conversion is a smart choice, both for the environment and for your business.
- Shorter time schedule. The delivery time for a new biomass-fired boiler is typically between 24 and 30 months. A fuel conversion on a coal-fired boiler, on the other hand, can typically be done within 4 to 12 months depending on the complexity, operational requirements, boiler size, etc. The re-use of an existing boiler and boiler house typically only means minor modifications to building and emission permits, which significantly shorten the processing time with local authorities. The entire process of fuel conversion, from order to operation, can be as little as 18 months, giving you a much quicker return on investment.
- A fraction of the cost of a new boiler. For most industrial boiler owners, reutilising existing assets is the most desirable course of action. Converting an existing boiler is typically only 15-30% of the cost of installing a new biomass-fired boiler, thanks to the re-use of steelwork, heating surfaces, ducting, fans, pumps, and piping. It is also likely that most parts of the coal transportation and storage systems can be adapted for biomass and residues.
- Cleaner Operation. Biomass is a cleaner energy source than coal because it does not contain significant amounts of sulphur, nitrogen, particles, and ash. Additionally, biomass allows for lower levels of CO and NOx emissions, without the need for extensive flue gas treatment equipment (except in the case of waste wood).
- Operating Cost Savings. For several years, the cost of biomass and residues has been decreasing while the cost of coal has been increasing. By using biomass instead of coal, facilities will have a cheaper source of fuel while also eliminating the operational, maintenance and environmental costs associated with the storage and handling of coal and ash. With less ash carry-over, biomass minimises ash build-up, which reduces heat transfer, meaning the boiler can maintain its efficiency.
- Reduced CO2 footprint. Unlike the burning of coal, which releases carbon dioxide into the atmosphere, the use of biomass and residues as fuel is a carbon-neutral way to power your cogeneration plant. In addition to switching to a cleaner source of fuel, additional carbon emissions are saved by re-using your existing assets rather than having new ones built and transported.
- Sustainable solution. By re-using the existing assets of your current coal-fired boiler, the boiler house will likely only need minor modifications to switch to biomass and residues. You may only need to modify the furnace, superheater and economiser and add one or two new tube banks. Through the re-use of the existing boiler, boiler house and fuel handling system, very little material will go to waste. The smart use of existing material can be a strategic focus for some companies – an example of which you can read about here.
- Less use of abatement materials. If the retrofit is based on reusing the existing boiler and flue gas cleaning system, the local authority issuing the operating permit will likely categorise the boiler as an existing installation, resulting in less stringent requirements on emissions and operating conditions of the plant. This means higher allowed emission limit values (ELVs) and therefore less use of abatement materials for the flue gas treatment. If the modifications to the boiler and flue gas cleaning system are more extensive, or if systems are replaced, the local authorities might set ELVs as if it was a new installation.
RELATED: From coal to biomass: Clean district heating, fuel flexibility and operational savings
If you are considering converting the fuel source of your existing boiler, you can read much more about the process, its benefits and case studies in our e-book ‘Fuel Conversion: Converting from coal to biomass and residues to improve sustainability’.
Do you need help with your project?
Our experts are ready to assist you. Fill out the form below and we will get back to you as soon as possible.
Contact us
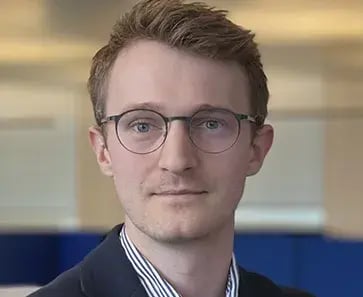
David Kjølby Krøger
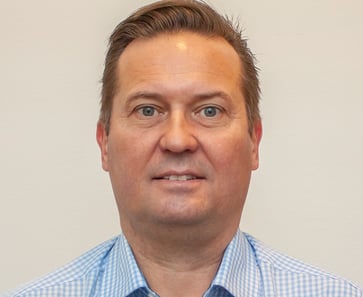